Painting color, finally!
It seems like it’s taken ages too long to get to this point, but the body is finally sporting Opalescent Dark Green instead of blotchy primer grey! It’s been nearly two years since the boys and I fetched the car from Virginia, and it is only now on the way to coming back together into car-like shape.
I don’t think it’s worth going over the tedium of sanding the bonnet (endlessly!), except to say that the process forced me to head to the paint shop for another quart of high-build primer. That last quart barely made it, too. To count the quarts of primer I’ve sprayed, you’d think that the car body would be little more than a large clump of primer, but that’s not the case. Most of the primer ended up suspended in water in a bucket after being wet-sanded off the body. I do think that my inexperience made the block sanding a little more difficult and protracted than would be the case in a real body shop.
If there is a science to block sanding, it has to be a matter of using the longest sanding board that you can manage on the space. I think the depressions that I ground into the primer — only to refill them with yet another spray — came about because I used either a short block or I used a too flexible styrofoam block at the wrong time. The persistent waves on the bonnet’s wings were conquered after I only used my long firm sanding board. (The picture above appears to show some wavy light lines to the right of the performance bulge. Those light lines are bowed because of the pressure of the bonnet sitting on the sawhorse underneath. When it’s not mounted on sawhorses the bonnet itself is straight, thank goodness!)
All surfaces of the car have been sprayed with color now, with the exception of the exterior sides of the doors and the trunk/boot lid and the gas filler cover. These final parts will probably be sporting Opalescent Dark Green after the Labor Day holiday in September.
Body shell color
The body shell took color well into August, and really the body shell didn’t take much time in August to prepare since most of the work had already been done. In July, I sprayed the final coat of high-build primer, and then I pretty much let it sit. The only preparation was sanding the wings lightly with a flexible styrofoam sanding board and them paying much more attention to the sills. I used the long sanding board on the sills, and this final prime/block-sanding took out the last of the ripples.
So, when it really came down to doing the job, the first part was masking. Since I had already sprayed color on the interior, inside the boot/trunk, inside the gas tank filler hole, and on the front bulkhead/firewall and subframes, those were all masked off. The borders of the already painted areas were scuffed with steel wool, and the masking tape exposed a small section of the already painted area. The narrow painted areas would get another coat of seal, basecoat, and clear. I figured it was worth coating these areas twice, just to make sure that color was uniform, and no lines of primer appear in the final product. These sections were all in “channels” so they are unobtrusive or obscured by rubber seals.
The process of masking took far longer than I anticipated. The easiest was the firewall/front bulkhead section since it was pretty much a straight shot. The trunk/boot area and the interior were more difficult because tape needed to be pressed from behind the plastic sheeting. I usually outlined the area with wide masking tape and then pressed plastic sheets onto the outline. The masking picture to the left shows the finished product. I used plastic grocery bags on the “A” posts, and Costco paper towel packaging served as the plastic covering for the trunk/boot area. The interior was draped in garbage bags that were cut along the heat-sealed edges to make large thin plastic sheets. I found that the thicker “drop cloth” plastic that you get at the lumber yard was simply too thick and not pliable enough to work with easily. (I ran out of 2-mil plastic sheet, and that worked very well, I should say.) The gas tank filler hole was just taped, no plastic needed.
On the masking tape: I don’t recall the wide selection of masking tapes a few years ago. Perhaps there were indeed time-rated masking tapes of various colors at paint shops, but I never ran into them. For this masking, I unsuccessfully tried a purple masking tape whose adhesive was supposed to be good for up to a month without drying out. The adhesives, apparently, can cause damage if you leave them on too long. I will admit that I have run into very old dried masking tape that’s been a bear to get off without damaging the underlying paint.
Well, kinder and gentler masking tape is a very fine idea, but the stuff has to stick in the first place. My experience with the purple masking tape was that it stuck at first, and then let loose with the slightest of pressure (like the blow of air from a paint gun) or it simply pooped out and let loose. My suggestion on the time-rated tape is to use the regular sticky beige masking tape, which I was told was good for “no more than four hours.” Unlike the purple stuff, the regular masking tape sticks. Although it’s worth taking it off as soon as you can, I’ve not had trouble with it damaging underlying paint even after several days. Leave it on for weeks, and you might have trouble. I noticed that Bill McKenna used the purple stuff when he was masking his E-type coupe for painting. I don’t know what he thinks about it, though.
The paint process, as before, entailed careful cleanup, spraying sealer, spraying basecost, and finally spraying clear.
I was a bit concerned about any wrinkling in areas where the paint might resist sticking, as I had run into before. Clearly, this is a surface preparation problem, and I think I ran into it because I did use a silicone-based sealer on some weld points. That should not be an issue on the body exterior anywhere, but I was careful to clean the primed surface with clean water, which I then dried with lint-free towels. This left the surface without any dusty primer residues from sanding. Next I used a “liquid deglosser/degreaser” that I have seen remove oils and grease quite effectively. I picked it up at Lowe’s so it is not anything special — just a typical brand. The degreaser is quite volatile, so it evaporates quickly. Then, after about an hour or so wait, on goes the sealer. The process is the same as before.
We departed from the previous paint sessions by blocking the completely dried clearcoat with 800-grit wet sandpaper. This wasn’t done immediately; I waited ten days to take it on. Because the surface was well shaped, there were no areas where I sanded through to the basecoat. I used a fairly small block of medium stiffness styrofoam (actually it was 3/4 inch foam insulation). For areas where I detected runs in the clear, I used either a section from a wood paint stirring stick wrapped in 800-grit or a small hard rubber sanding block to focus on the high areas. When I talked with the people at my paint shop, they were concerned that the clear was thick enough. If you do sand through to the basecoat, I was told, “you end up with a mess.” They advised that at least two coats of clear be on the surface before sanding. I didn’t count the coats on the car body, but I know that we resprayed the clear after the original coat had set a while. So, I wasn’t worried.
This post-clearcoat sanding was not a tenth as onerous as blocking primer, and a third as messy. The clear is much, much tougher than high-build primer, naturally, and so the mess is small. You end up with a thin lather of suspended clear over the surface, and the unfortunate orange peel or run ripples are easy enough to remove.
Bonnet color
As I’ve said before, the E-type bonnet makes up much more than even its formidable size in the imaginations of car enthusiasts. The bonnet itself comes close to expressing the most special qualities of the E-type. So, when it came to applying color, painting the bonnet meant really painting the car. And we wanted it to be perfect. But we did run into disconcerting troubles before we finished the job.
The bonnet came in from the outside where the interior was sprayed with color after all the rock guard and primer had gone on. I believe that we can finally dismantle the old rolling rack that held the car shell for over a year. (We made the rack from wood salvaged from a humble old chicken coop. So, I guess one could say that instead of finding this car in a chicken coop, this one was on top of one for more than a year.) We put the bonnet on saw horses that fit to each side of the performance bulge and nearly touching the inner duct wings. This was a mistake. Or, at least the way we set the bonnet on the horses was a mistake. We didn’t pad the points where the bonnet and the sawhorses met, and we discovered that the weight of the bonnet pushed the metal out at the forward-most points of contact. On the left side, this was a gentle bulge that disappeared when we lifted the bonnet from the sawhorses, but on the right we have a little touch-up to do. I think we’ll be able to press out or gently knock out a persistent bulge on the left side. Aaron noticed the bulges when we were rubbing the bonnet with steel wool (for reasons spelled out later). They were unfortunately not visible at the time we set the bonnet on the sawhorses.
The Moral: If you use sawhorses to suspend your bonnet, make sure that you have the sawhorses well padded, and I think fashioning a broad supporting plate from plywood is advisable. You need to spread the weight resting on the sawhorses.
I mentioned steel wool. Here’s the story — another mistake that a little research solved, but that could have been messier to deal with had we continued with the painting process. After the sealer and the basecoat was applied, we noticed that the basecoat was drying “cloudy,” as if it had been lightly covered with a whitish-grey spray. This was only apparent after the basecoat had dried, and the cloudiness was not uniform across the surface of the bonnet. In general, it followed wide lines of the spraying itself, usually appearing where there was probably an overlap of spray.
I had not run into this on other surfaces, and I initially thought that the cloudiness might be resolved when the clearcoat was applied, since the clear is supposed to melt and resuspend the base. But I wasn’t sure, so I searched the web and found that this is a common phenomenon that is usually caused by thinning the basecoat too much or by applying clearcoat before the basecoat has dried sufficiently. The “cloudiness” is actually suspended flakes that float to the surface of the too-thin paint. The recommendation was to reshoot base on the surface, making sure that the basecoat paint was accurately thinned. Not too much, not too little — just right.
I took a little fine steel wool after a cloudy section, and the clouds disappeared with a little rubbing. The integrity of the basecoat (which dries very soft) was unassailed. Aaron and I rubbed the entire surface of the bonnet with steel wool to dispel the clouds, so to speak. After that, Aaron cleaned the surface with compressed air, and I sprayed another thin coat of basecoat over the bonnet. It dried as expected, and then the clear went on. We let the clear set for about a half hour, and then sprayed a second coat over the almost-dried first coat. It was a bad oversight on my part to have missed taking a picture of the clouded basecoat. If it happens again, and I hope it won’t, I’ll remember to take a picture. You can imagine that things were a little tense around the old DeLong hacienda as the bonnet clouded up!
The bonnet will get the 800-grit sanding treatment in mid-September, about two years after we initially rolled the car into the old cat cage garage.
The photos below show the bonnet in primer, basecoat (after steel wool treatment) and after the clearcoat. You can see one of the door panels to the rear of the bonnet. The interior sections of the doors and the trunk/boot lid were painted with the bonnet.
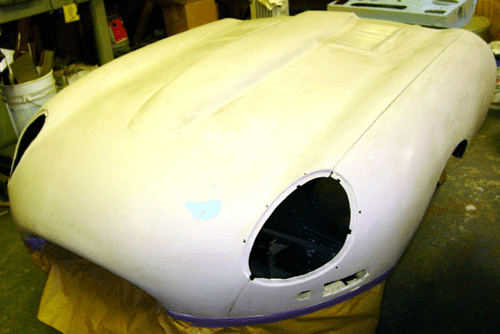